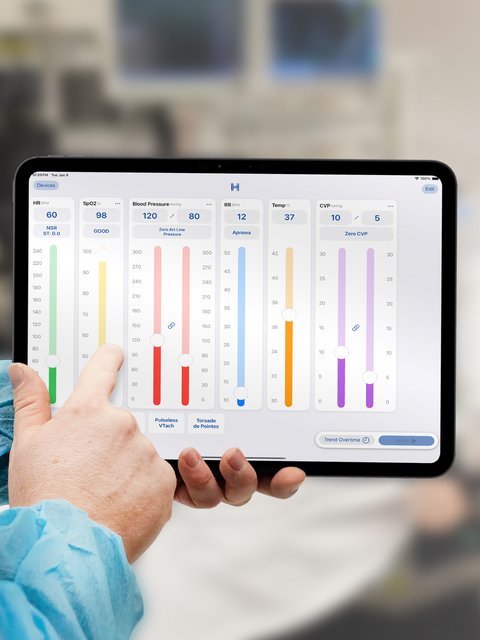
Hartwell Simulation: Hartwell Simulation System
Taking medical simulation to a new level of realism.
The software problems we solve come in many shapes and sizes. Sometimes, customers start building a tool, get stuck, and look for answers. Or they’ve built something that works well but could use a little help with those final technical and design hurdles. That’s the situation Hartwell Simulation CEO Michael Sheedy found himself in when he approached us in 2022.
Michael is based at Christchurch Hospital. His main role is heading up the bioengineering team, a group of mechanical, electronics and software engineers, technicians, and developers. Their job is to design bespoke solutions to meet the needs of the medical specialists who work for HeathNZ – Te Whatu Ora.
Michael explains, “We’re here to enable medical experts by giving them the necessary tools. We can modify an existing device or make one from scratch. Often, we’re bridging the gap between the devices delivered by medical companies and the diverse needs of our patients.”
Michael and his team make everything from bespoke surgical retractors to titanium plates for skull implants. They also support clinical simulations. Simulations allow clinical teams to practice resolving medical scenarios in a risk-free environment to help them deal better with real-life situations. Simulations are invaluable for medical students and clinical teams use them to upskill. Various devices are used to simulate medical scenarios, and the bioengineering team help maintain the tech for these tools.
The importance of realistic clinical simulations
In 2014, Michael met anaesthetist Dr Dan Hartwell. He says, “Dan needed some help to run simulations within the hospital working environment.” Simulations can be run in dedicated centres or in situ in hospitals. Michael points out simulation centres are great for working on teamwork and communication; however, they fall short when recreating technical problems. He explains, “The trouble with simulation centres is they use fake monitors, which aren’t the same as real monitors in surgery. It’s like training a pilot in a Boeing 747 and then chucking them in an Airbus. The flight controls are completely different.”
Dan solved this issue by running simulations in a surgical environment using a real anaesthetic monitor to train students to respond to the machine's changing cues. He’d even worked out how to use biomedical calibrators to replicate a patient’s heartbeat, blood pressure, respiration rate, and oxygen level on his monitor.
However, calibrators aren’t designed to alter inputs dynamically. So, Dan was conducting simulations by adjusting pulse, respiration, and oxygen saturation on three different calibrators in front of him. Michael says, “We likened it to Dan being a DJ playing a set. He was doing a great job replicating a lifelike anaesthetic scenario, but it was very stressful, took a lot of set up, and was difficult for someone else to pick up and do.”
Taking their game-changing prototype to market
Dan acquired a new device that calibrated blood pressure, heart rate, and oxygen saturation. This was a big step forward; however, it was designed for calibrating equipment, not running a simulation. Dan still had to navigate between menus to change heartbeat or oxygen level. So, Dan asked Michael for help to develop a single interface he could use to simulate a lifelike response to clinical decisions.
Michael says, “I took on programming the new interface, taught myself how to code and worked closely with Dan and other hospital clinicians to design what they needed in a user interface. We wanted an intuitive, easy interface, so people could instantly understand what it did and drive it with very little training.”
Once Dan and Michael got the prototype for the new simulator up and running, they saw how much it improved the calibre of their clinical simulations. They quickly realised they had built something that could benefit the whole medical establishment and created a company to take the tool to market. However, they needed support to commercialise their prototype.
Michael recalls, “We’d built a prototype that worked really well and ticked those easy-to-use boxes, but it was fairly ad hoc in how it connected. I'm not a programmer, so whenever I wanted to make changes to the software, I had to spend hours weaving my way through the code to change one bit. It made it hard to fix problems and evolve the device. That’s when we brought Smudge into the team to help us out.”
Supporting organisations to evolve tools built in-house
Michael’s goal was to take the software he'd created and turn it into something more sustainable, making it simple to do bug fixes and future customer upgrades. He says, “It was an easy decision to go with Smudge. The first time you met us, you visited a simulation in progress. The fact you were willing to come and see the simulator used within the clinical environment at that early stage spoke volumes about your commitment.”
At Smudge, we enjoy partnering with teams to evolve tools built in-house. And we're respectful of the work you’ve done. You’re industry experts. You know what you need. We spend so much time diagnosing and designing what organisations need in a software tool that we can tell when you’ve done that work well. We’re here to solve your problems, not reinvent your approach.
The Hartwell project was an excellent example because Michael had put so much thought into the simulator's user interface. It was a strong, functional design. We could focus on polishing other aspects of technical performance and user experience.
“Michael Sheedy“One great thing about working with Smudge was that you didn't come in and redesign the interface from scratch. You recognised there'd been a lot of work to get to the point we were at, and people were happy. So, you focused on the tricky stuff we didn’t know how to do.”
CEO, Hartwell Simulation
Effortless user experience takes a lot of effort
One challenge Michael and Dan had was getting the simulator to communicate reliably with other devices. They used an infrastructure-based Wi-Fi configuration that was great for prototyping but had some challenges when scaling production. We integrated Bluetooth LE to make that connection smooth and consistent.
The unseen experience is crucial in software design. When things just work and the user doesn’t have to think about it, it results from so many small decisions behind the scenes. Effortlessness takes a lot of effort but we've years of experience delivering that unseen attention to detail that makes the user experience feel great. With the simulator, it was about honing those edge use cases, such as connecting the device automatically to Bluetooth.
Michael says, “Working alongside Smudge, I've learned a lot of different approaches. You’ve taken the complicated tool I created and made a more elegant, simple solution so we can take the Hartwell Simulator to the next level.”
“Our driver now is to get this great tool out into the hands of medical professionals. By upgrading the software and adding Bluetooth connectivity, we’ve enabled high-fidelity in-situ simulations, taking this tool from a simple calibration device to a simulation system that can be used to train doctors and nurses in real-life environments. When it comes to a real medical emergency, we want our medical professionals making good decisions based on learnings from simulations that are true to life.”
Watch our interview with Michael Sheedy here.